6-Axis Robotic Arm
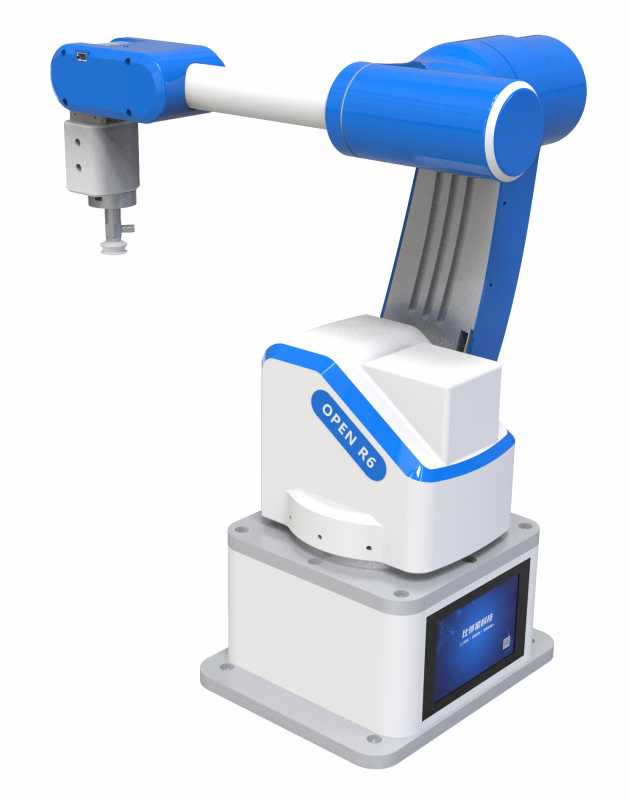
This robotic arm is a product specifically developed for education and scientific research. It fully opens up the mechanical arm structural design, motor control, and kinematic control algorithms, integrates open-source AI large model technology, and is compatible with advanced processors. Additionally, it offers multiple expansion interfaces to support the connection of peripheral modules such as vision, voice, and sensors, meeting the hardware development needs for various scenarios.
- Platform Integration Ready
- Multi-Robot Collaboration
- Scalable and Expandable
- Fully Open Source
- Cost-Effective Solution
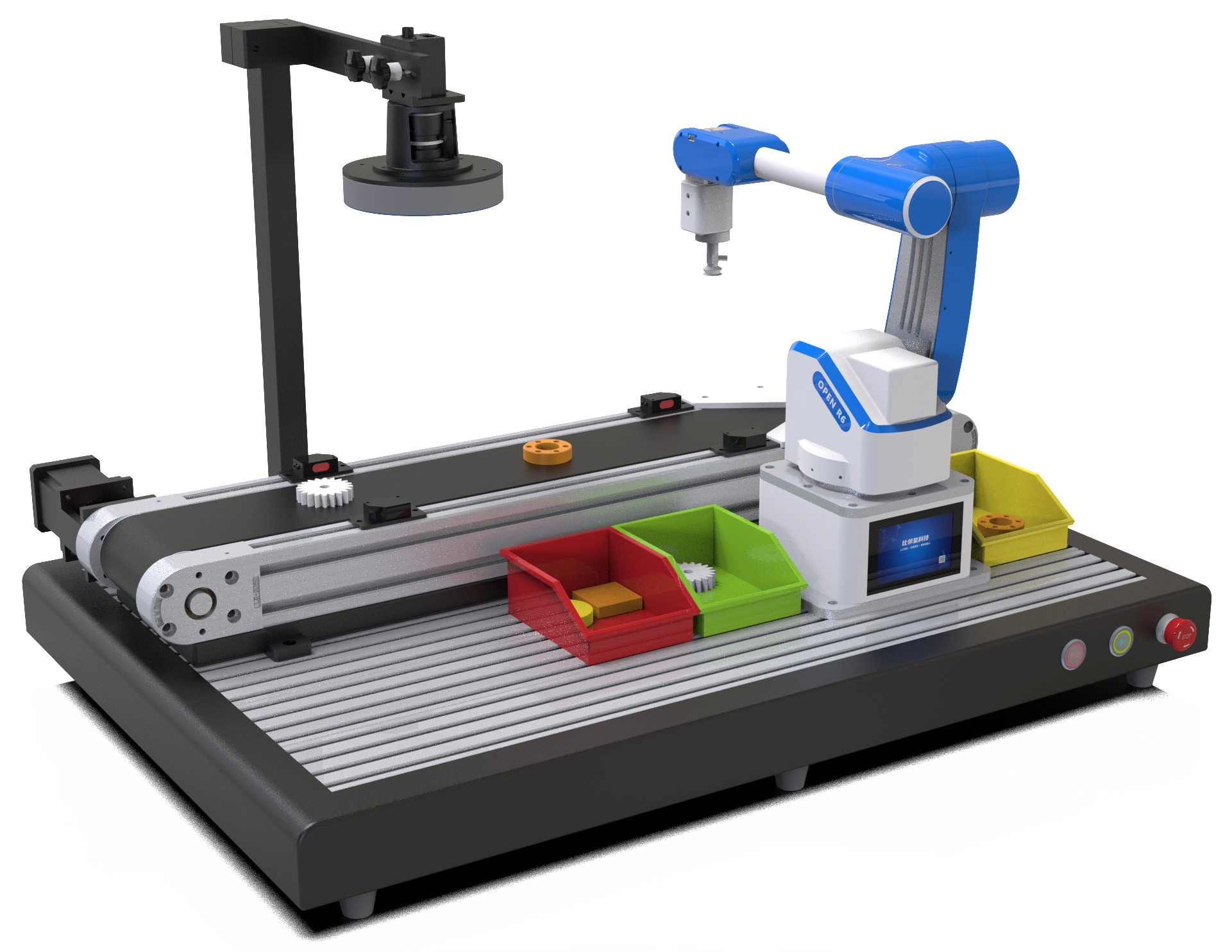
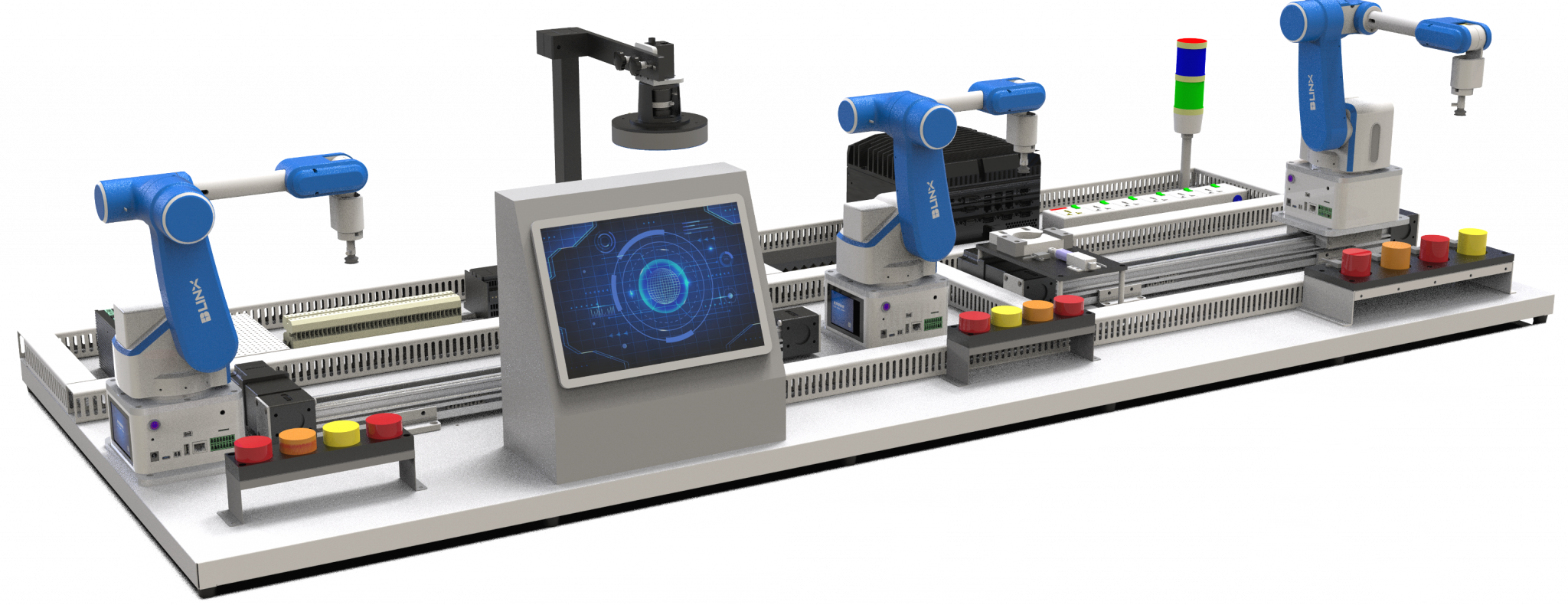
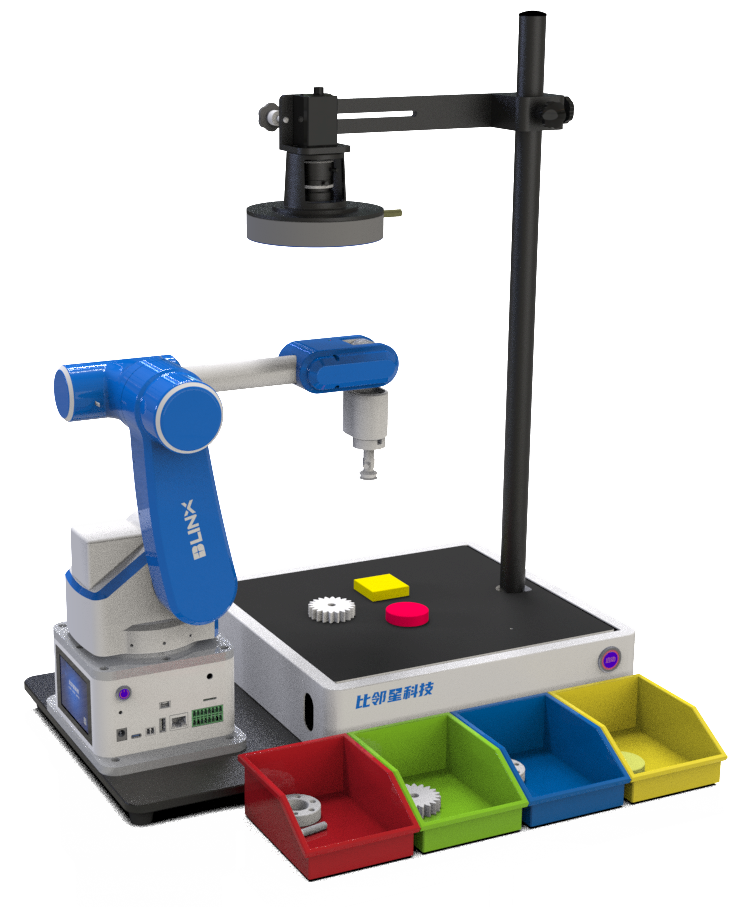
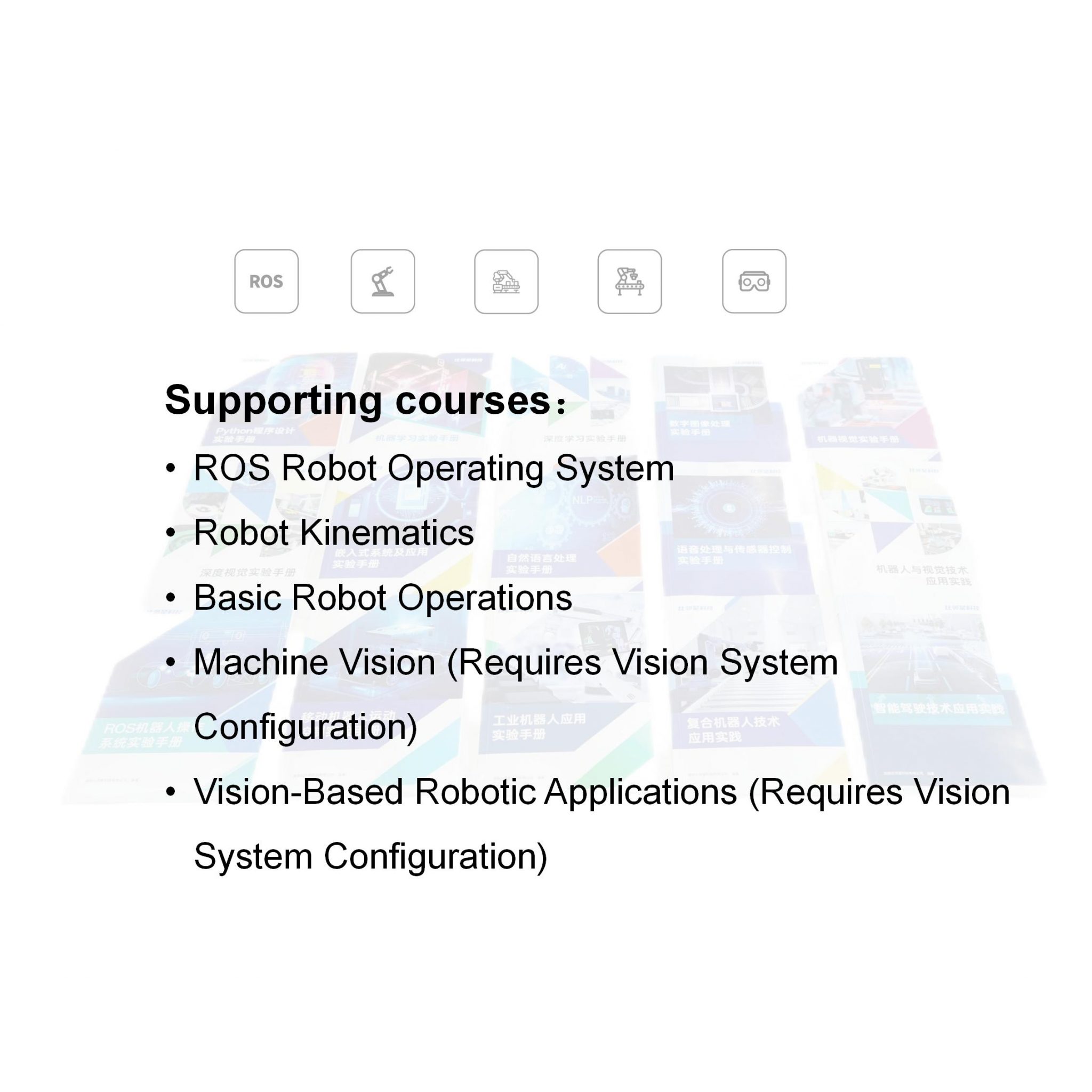
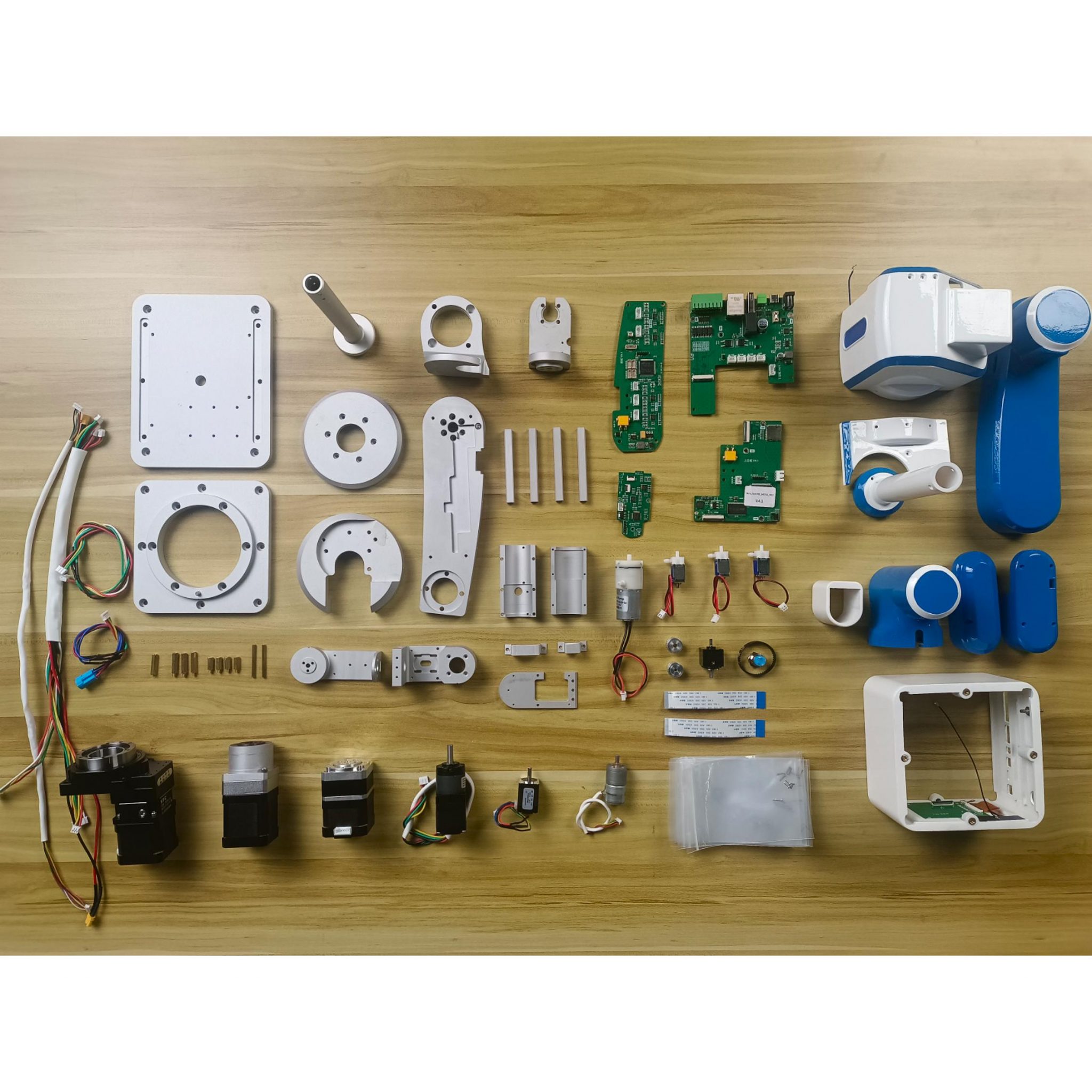
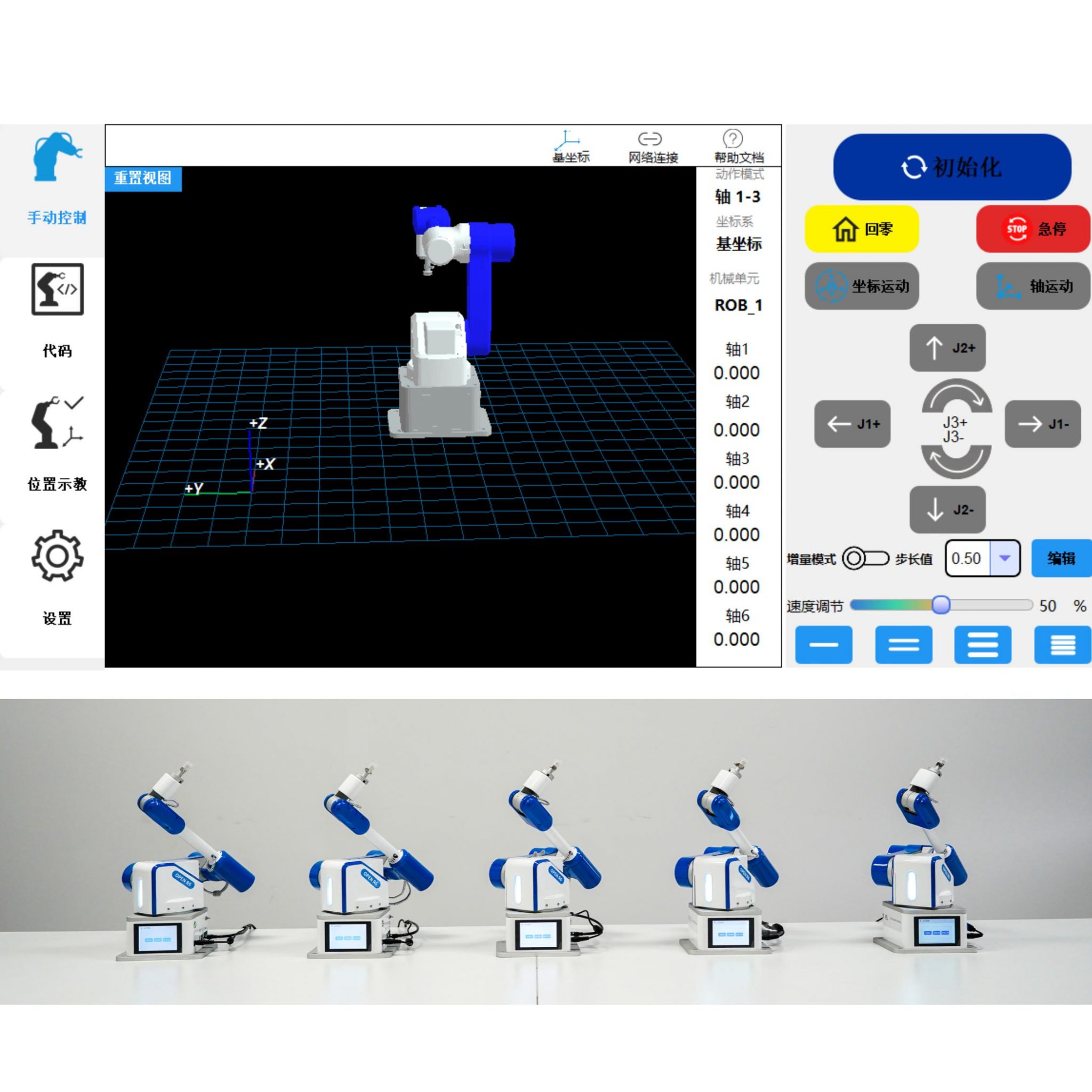
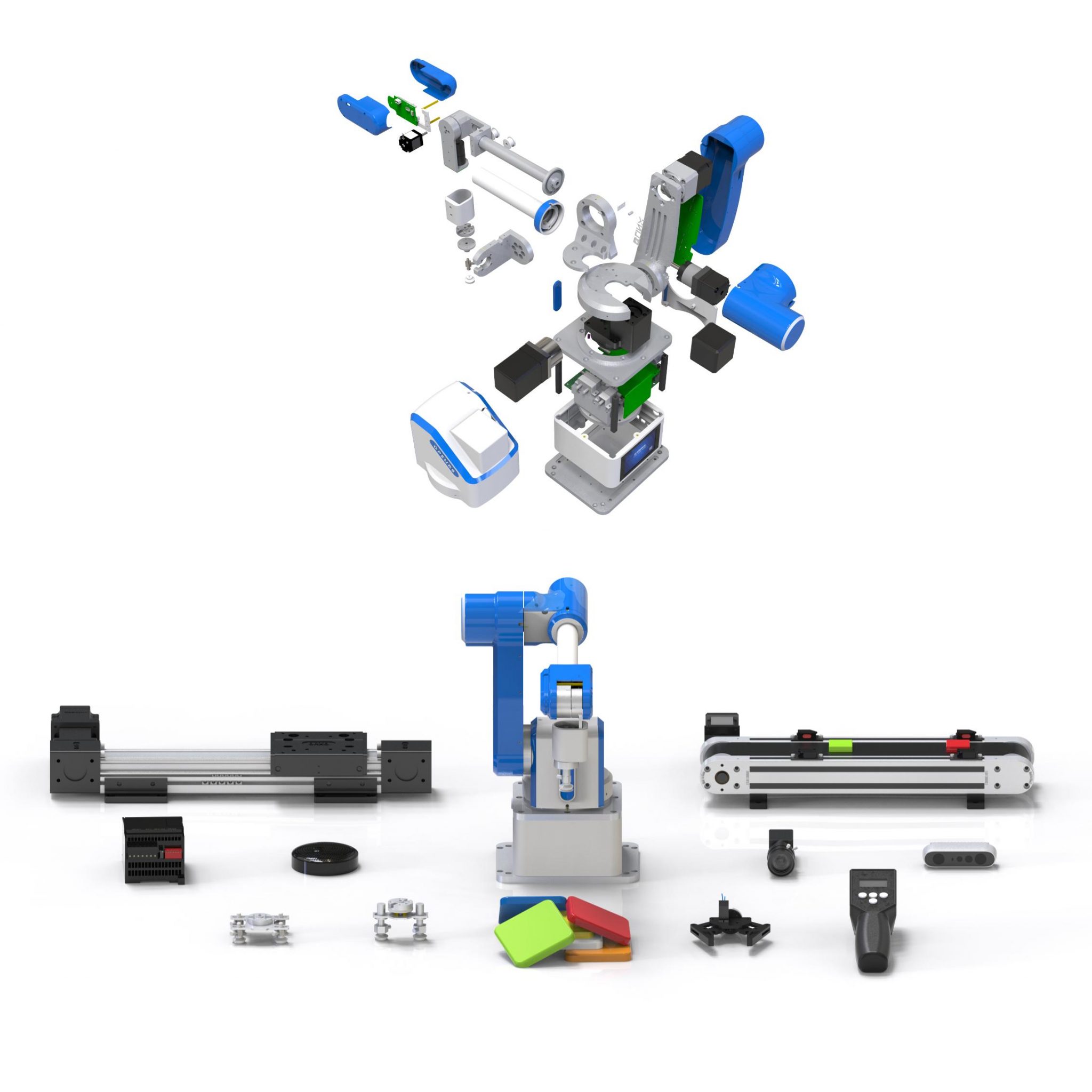
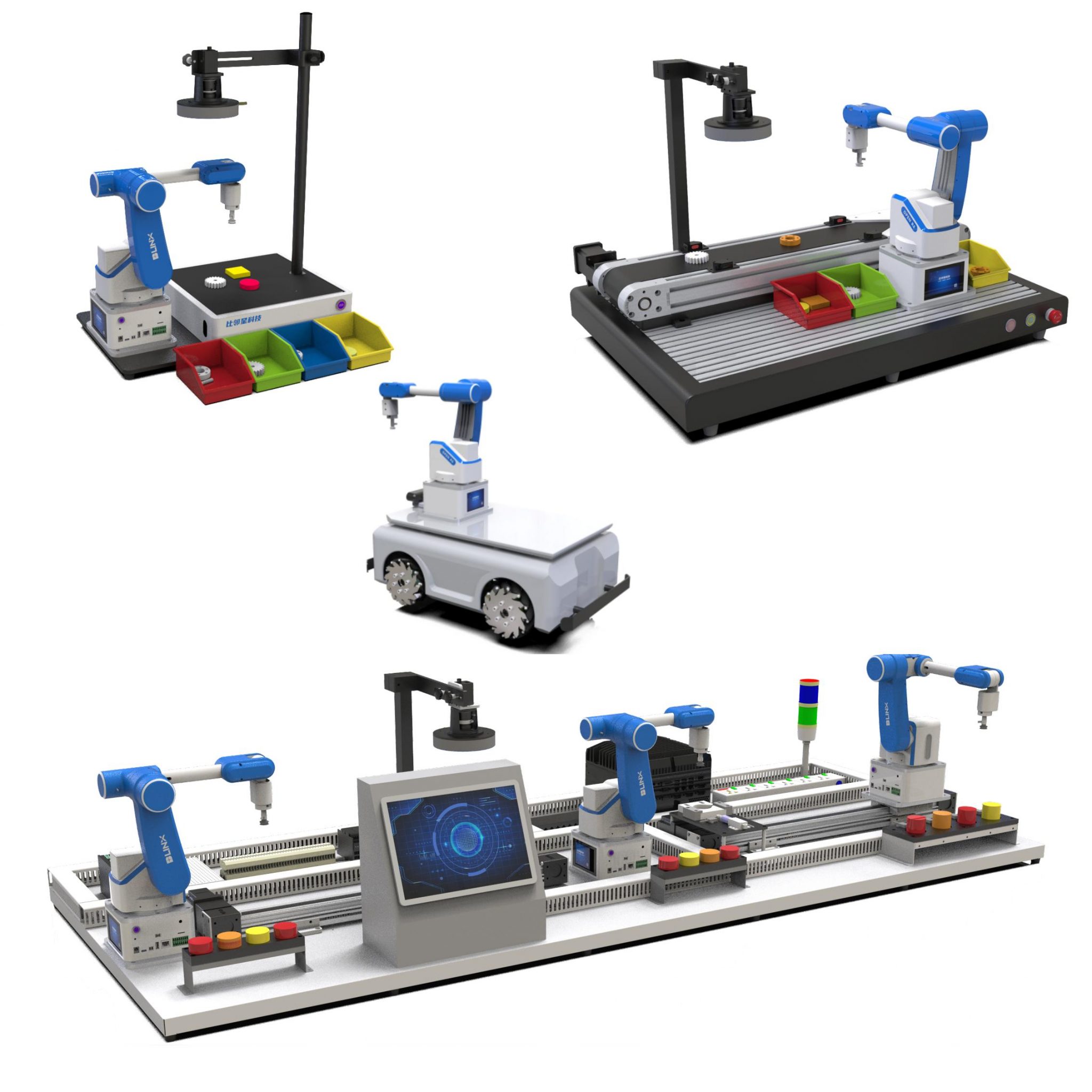
Specifications
Axes
6
Maximum Payload
1.0 kg
Working Radius
410mm(16.14in)
Weight
5.4 kg
Repetitive Positioning Accuracy
±0.5mm
Supply Voltage
12V/5A DC
Rated Power
60W Max
Material
Aluminum Alloy, High Toughness Resin
Working Environment
-10℃~60℃ (14°F~140°F)
Controller
STM32
Communication Method
USB/WiFi/Bluetooth/RJ45
Control Method
PC Software, Mobile App, Voice Control
Base Dimensions
170mm×135mm (6.69in×5.31in)
Axis Motion Parameters
(with a 500g payload)
J1:±130°,Maximum speed:45°/s
J2:-80°~+90°,Maximum speed:45°/s
J3:-85°~+40°,Maximum speed:45°/s
J4:±160°,Maximum speed:45°/s
J5:-179°~+15°,Maximum speed:27°/s
J6:±179°,Maximum speed:45°/s
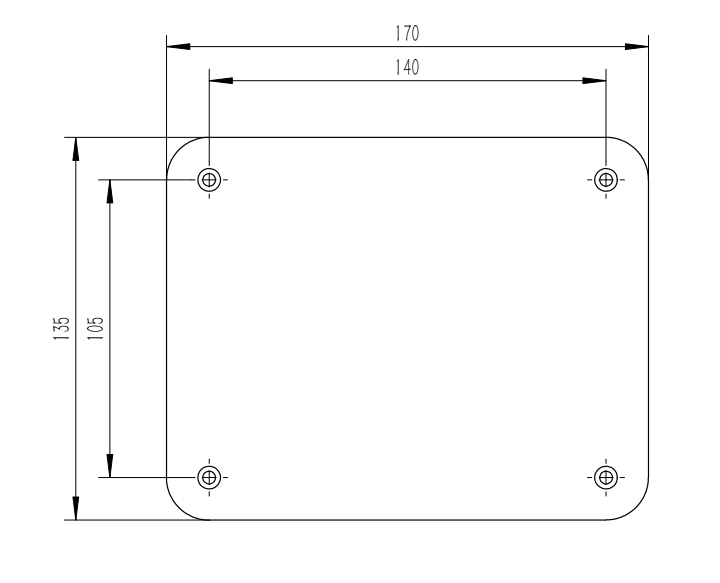
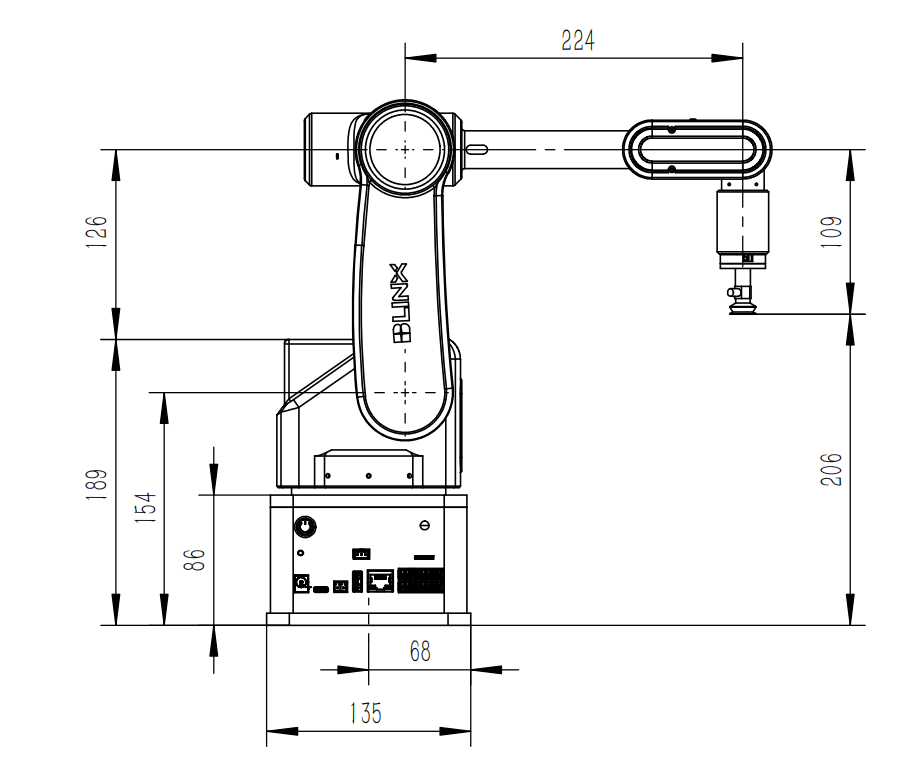
Video
6-Axis Robotic Arm
Remote control robotic arm
Suction cups and grippers
Description
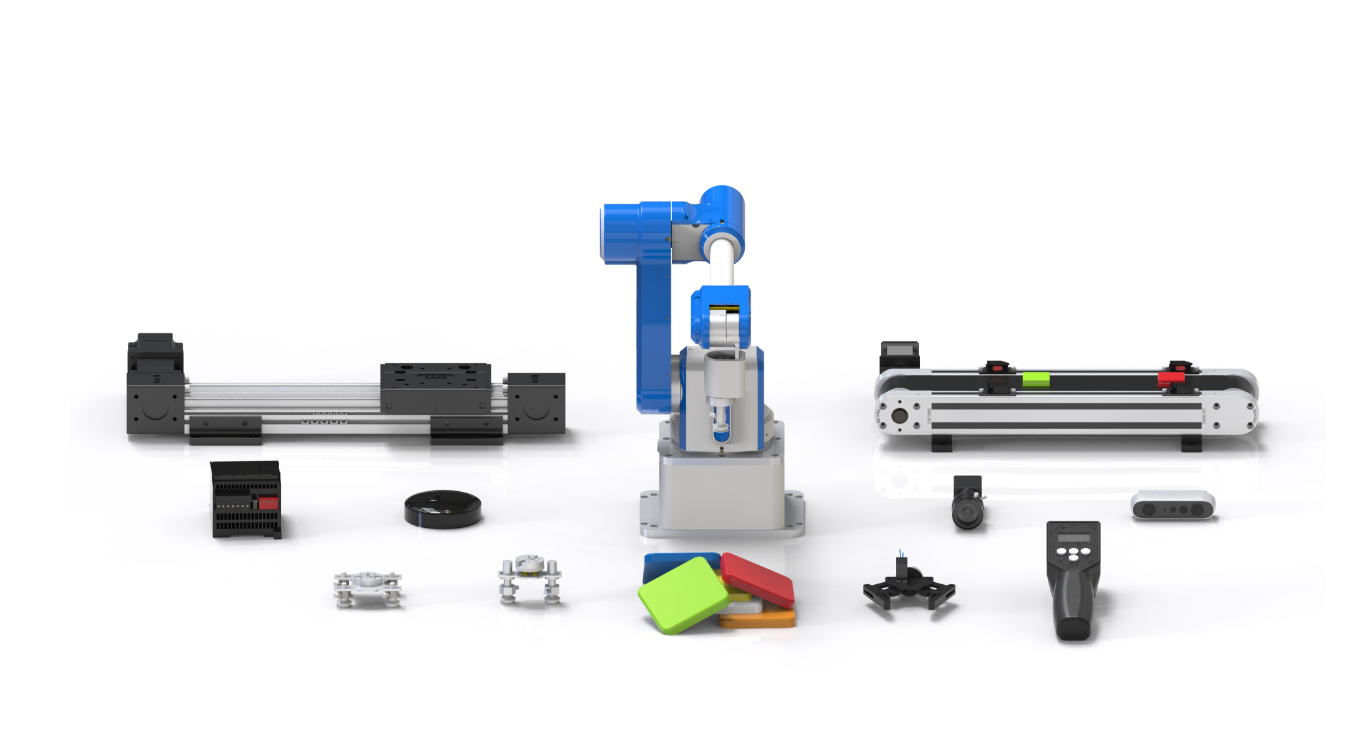
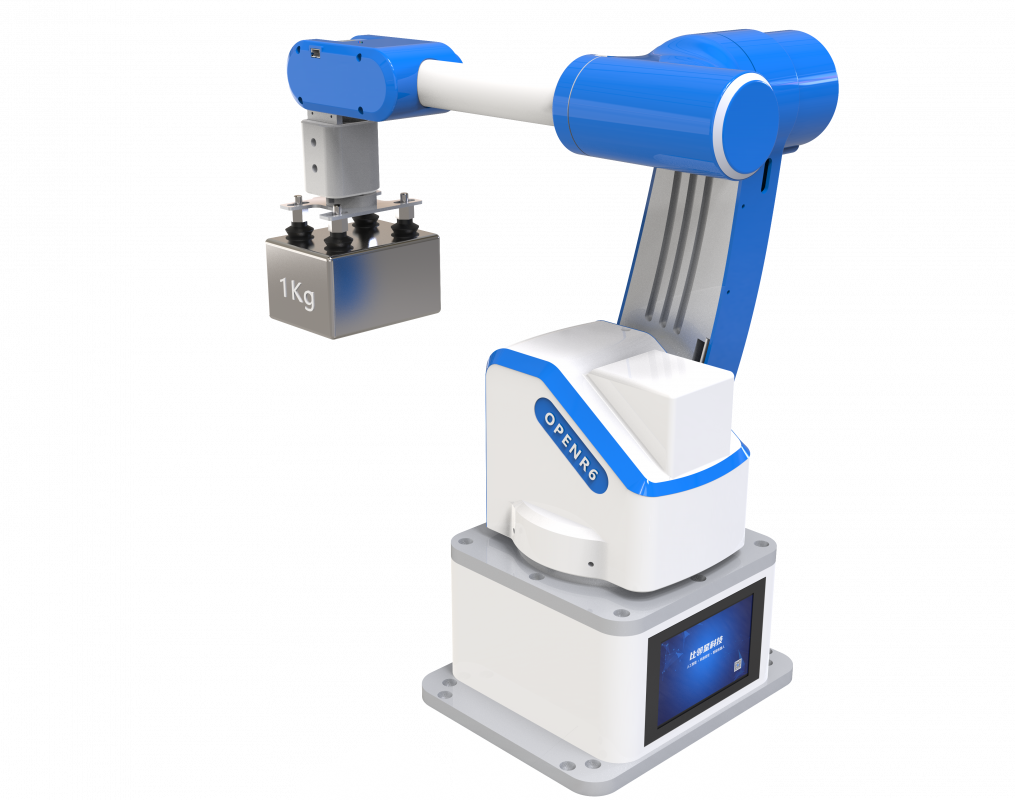

Suitable majors
1. Artificial Intelligence, Computer Science, and Related Fields
This focuses on the research and educational support roles of six-axis robotic arms in areas such as machine learning, computer vision, and human-robot interaction. Applications include enabling autonomous operation of robotic arms through AI algorithms and visual recognition-based grasping tasks.
Specific applications for teaching and research include:
Integration of Open-Source Large Models with Robotic Arms:
Understanding and applying open-source large models, multimodal fusion technologies, robotic arm control techniques, and real-time interaction and feedback mechanisms.SDK Training and Autonomous Programming for Robotic Arms:
Using and developing SDKs, creating and training SDK datasets, machine learning and reinforcement learning, designing autonomous programming frameworks for robotic arms.Deep Learning and Robotic Arm Visual Perception:
Deep learning models, computer vision technologies, visual servo control, cross-modal fusion and decision-making.Unordered Grasping with Deep Vision:
3D vision and point cloud processing, robotic arm grasp planning algorithms, compliant control for robotic arms, multi-object path optimization.Voice-Controlled Robotic Arms and Human-Robot Interaction:
Speech recognition and natural language processing, speech synthesis and interactive feedback, dialogue management systems, multimodal interaction fusion.
2. Robotics, Automation, Mechanical Engineering, and Related Fields
This emphasizes the application value of six-axis robotic arms in course instruction, laboratory training, and research projects. Focus areas include robotic motion control, simulation of automated production lines, design of end-effector tools, and mechanical manufacturing process practice.
Specific applications for teaching and research include:
Joint Control and Feedback for Robotic Arms:
Motor drive and control, sensor technologies, multi-joint coordination, intelligent control algorithms.Design and Development of Wireless Teleoperation Systems:
Wireless communication technologies, transmitter and receiver design, real-time communication reliability, hardware design and implementation of teleoperation systems.Multi-Robot Synchronization and Coordinated Control:
Coordinated control strategies for multiple motors, dynamic planning and optimization algorithms, fault detection and fault-tolerant control, real-time communication and information sharing.Visual Guidance and Robotic Path Planning:
Computer vision technologies, path planning algorithms, dynamic programming and optimization, real-time perception and decision-making.End-Effector Design and Expansion:
Design of end-effectors, material selection and mechanical analysis, intelligent perception and control, expanded applications and compatibility.
Expansion Capabilities
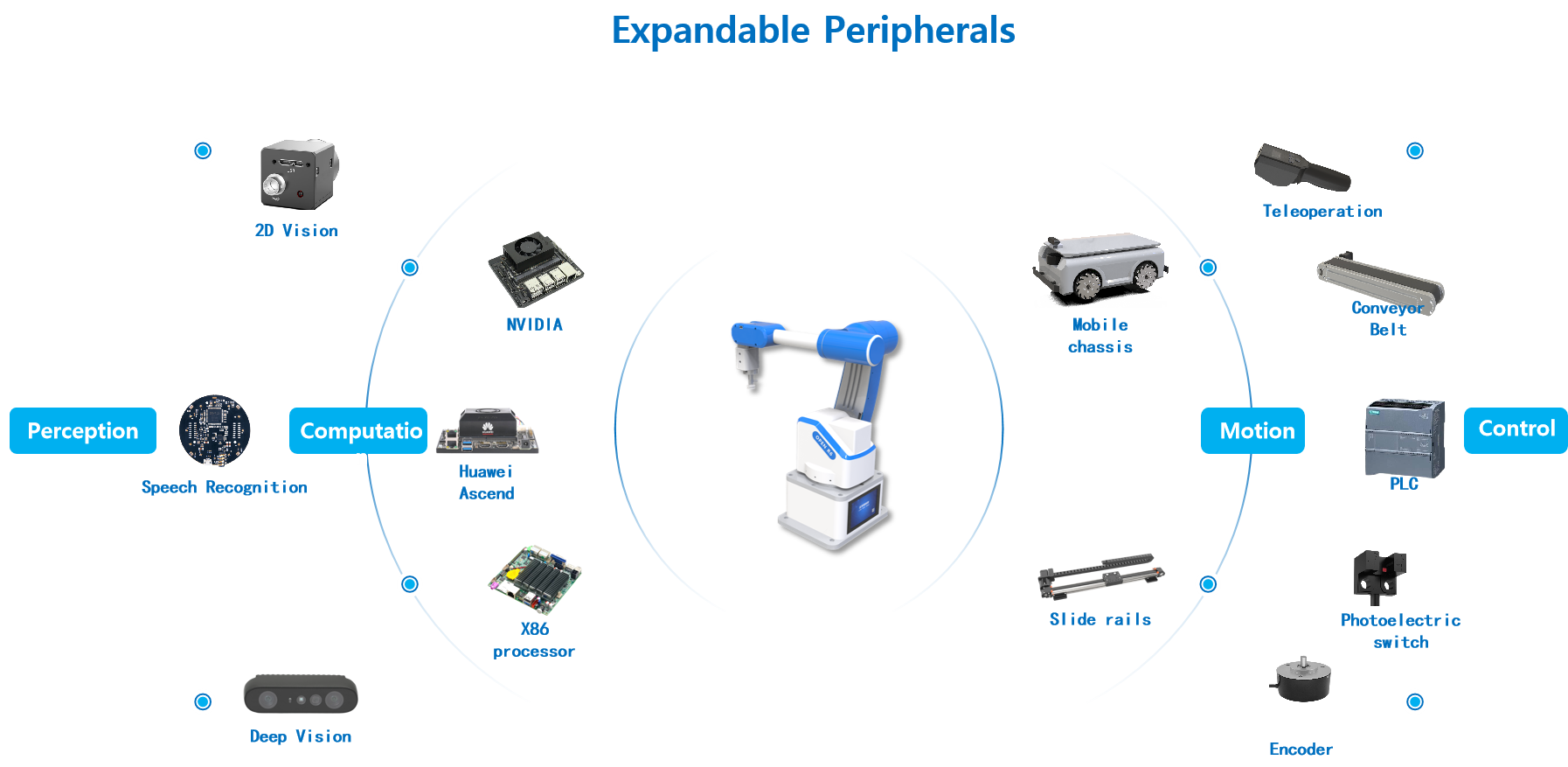
Features and Characteristics
1. Fully Open-Source Control
The structural design is provided with 3D model drawings. The motor control, along with the control source code for the motors, controllers, and robotic arm joints, is fully open. The kinematic algorithms are also open-source, including the forward and inverse kinematic models at the core level. Through comprehensive open-sourcing, users are empowered to engage in various research and development activities at both the hardware and software layers of the robotic arm.
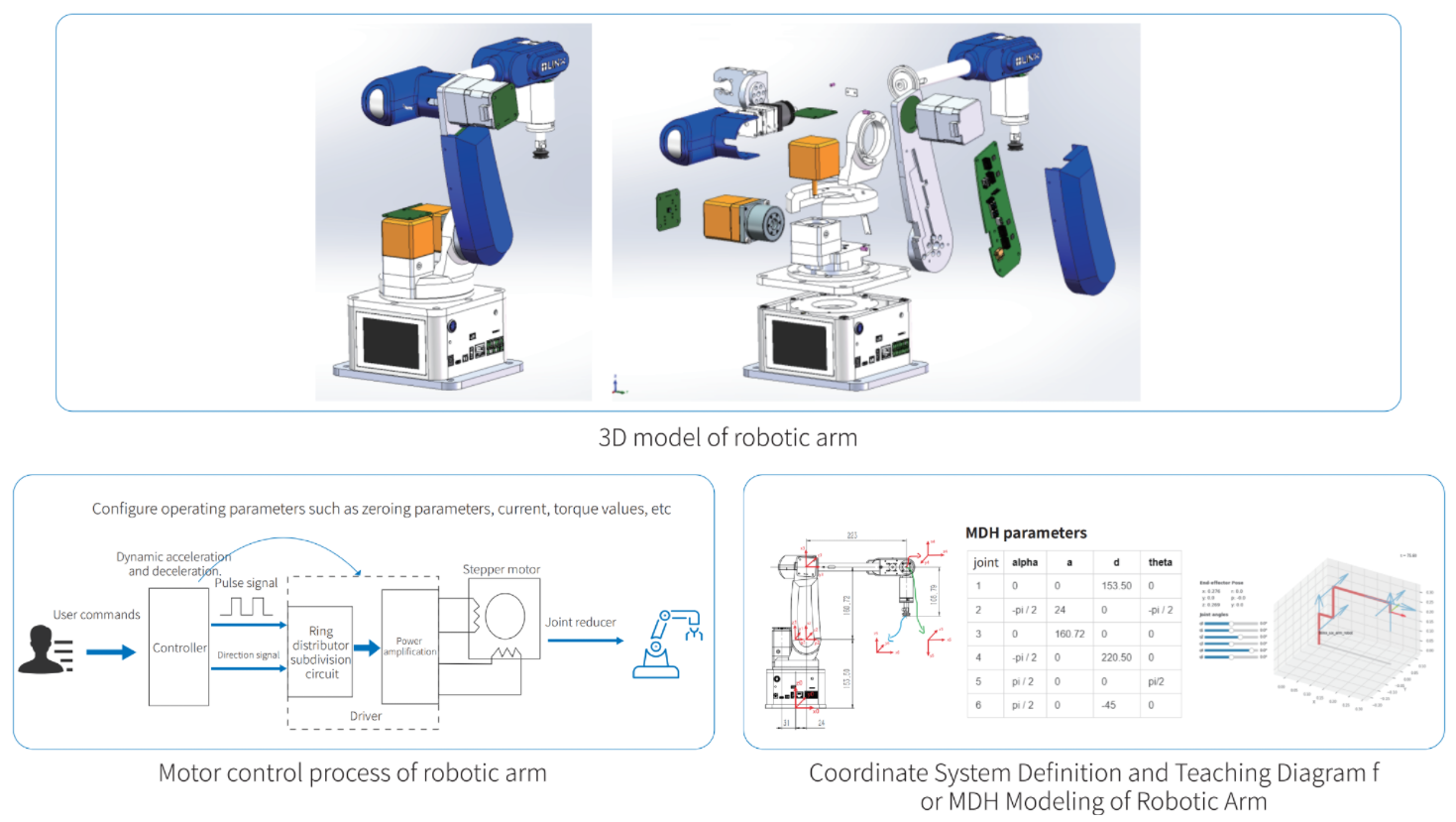
2. Visual Perception Capabilities
The robotic arm not only collaborates with traditional 2D vision systems but also integrates depth vision technology, enabling dual visual perception and cooperative operation. This greatly enhances the arm’s environmental understanding and positioning accuracy, allowing it to handle more complex task scenarios. Through depth vision, the robotic arm can more precisely recognize object shapes, distances, and orientations, enabling finer control over tasks and significantly improving its application value and flexibility. This drives innovation in automation technology.
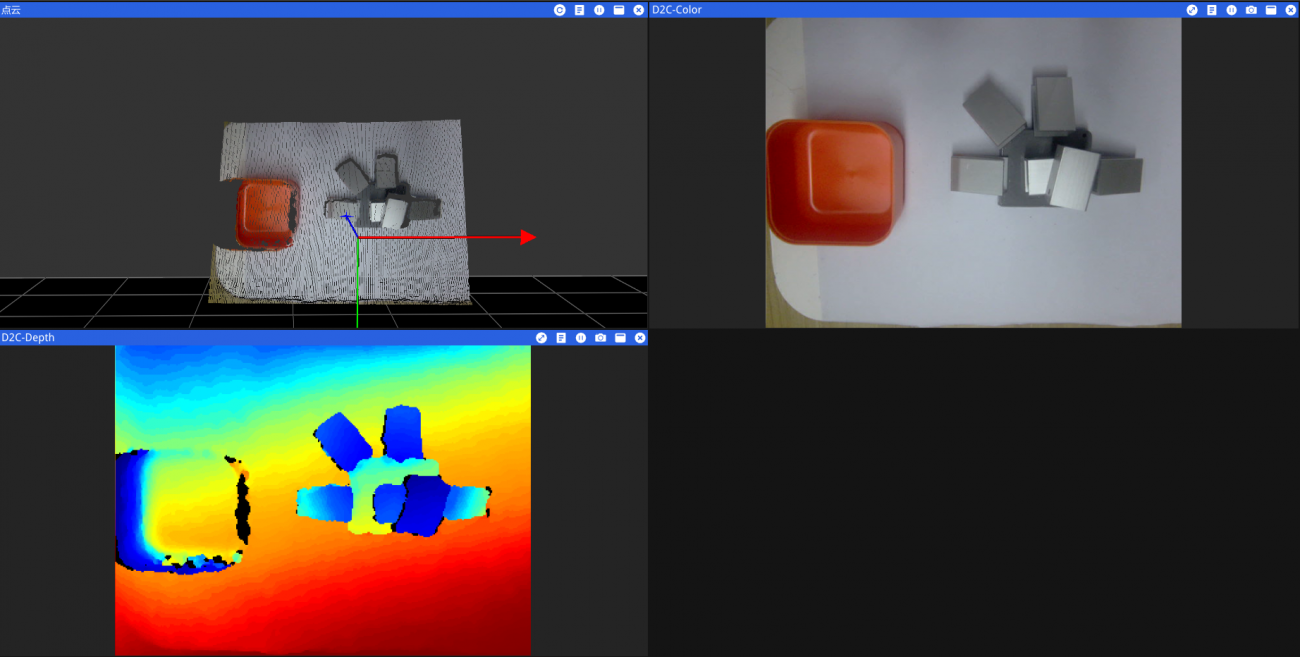
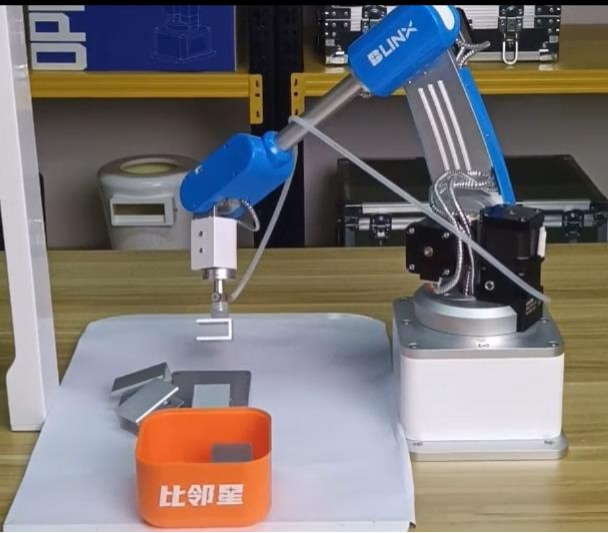
3. Integration of AI Large Models
The robotic arm deeply integrates with open-source AI large models. By training the arm’s SDK with AI large models, the robotic arm can autonomously write code and execute actions. Additionally, a complete end-to-end technology for AI model training is provided, including the integration of vision, voice, and other sensor data. This allows users to collect data, train, validate, and deploy models according to the specific application scenarios.
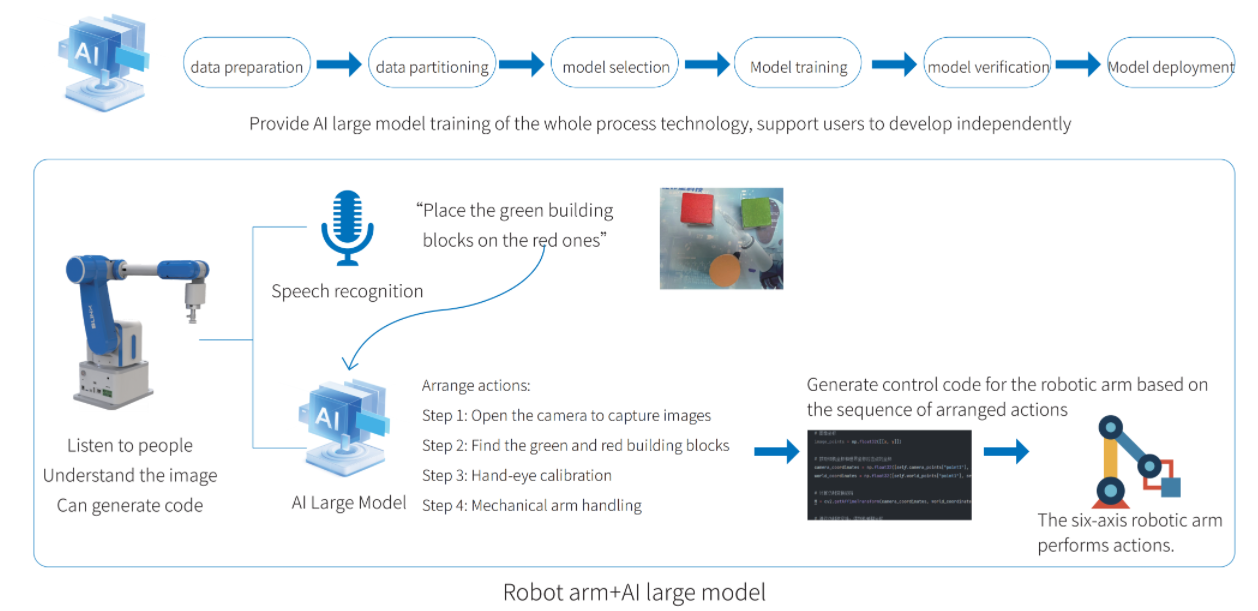
4. Support for Wireless Teleoperation
Equipped with an open-source teleoperation system, the robotic arm builds a reliable and realistic human-robot interaction environment, offering high-precision motion tracking, real-time dynamic force feedback, safety, and ease of use. These features make it highly suitable for applications in remote healthcare, remote services, space exploration, and other fields.
The system allows for the open access to core technologies such as sensor data collection from the teleoperation joystick, communication with the robotic arm, and SDK calls for motion control, thus supporting users in deeper learning and research.
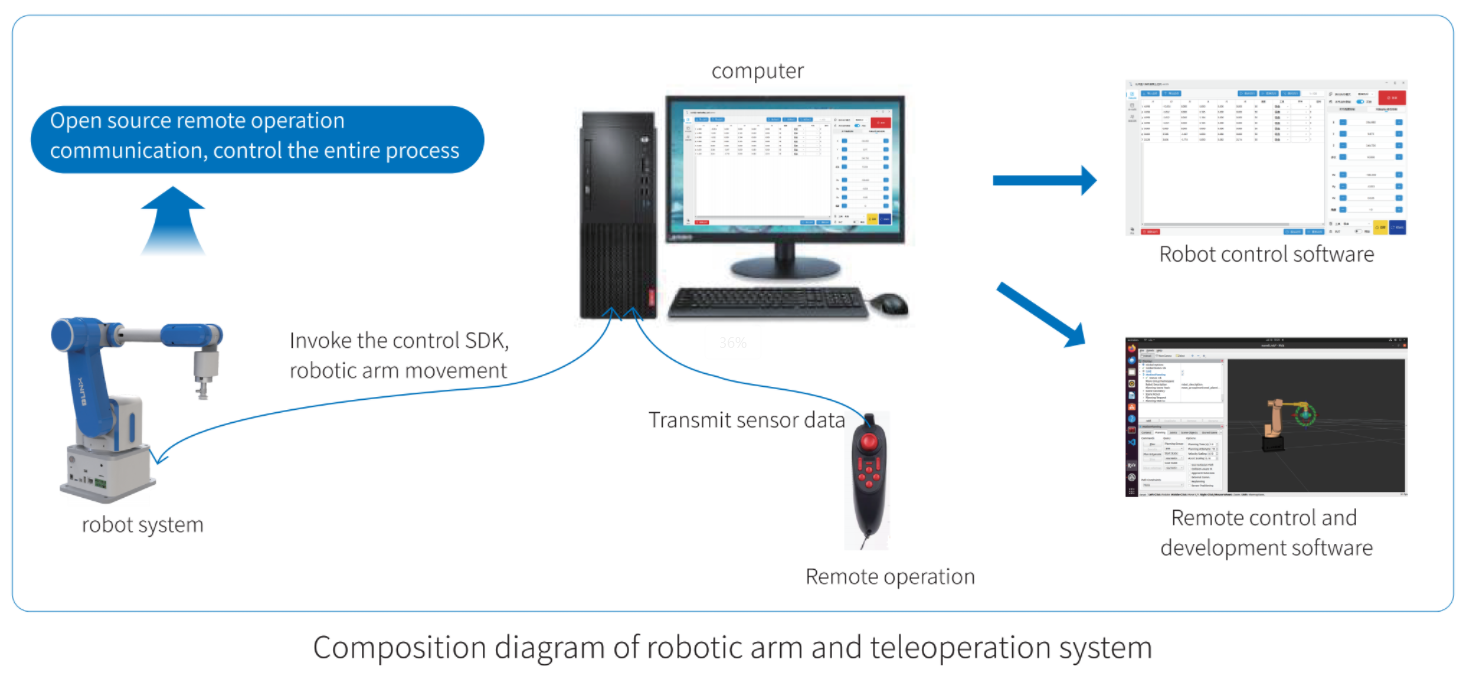
Courses
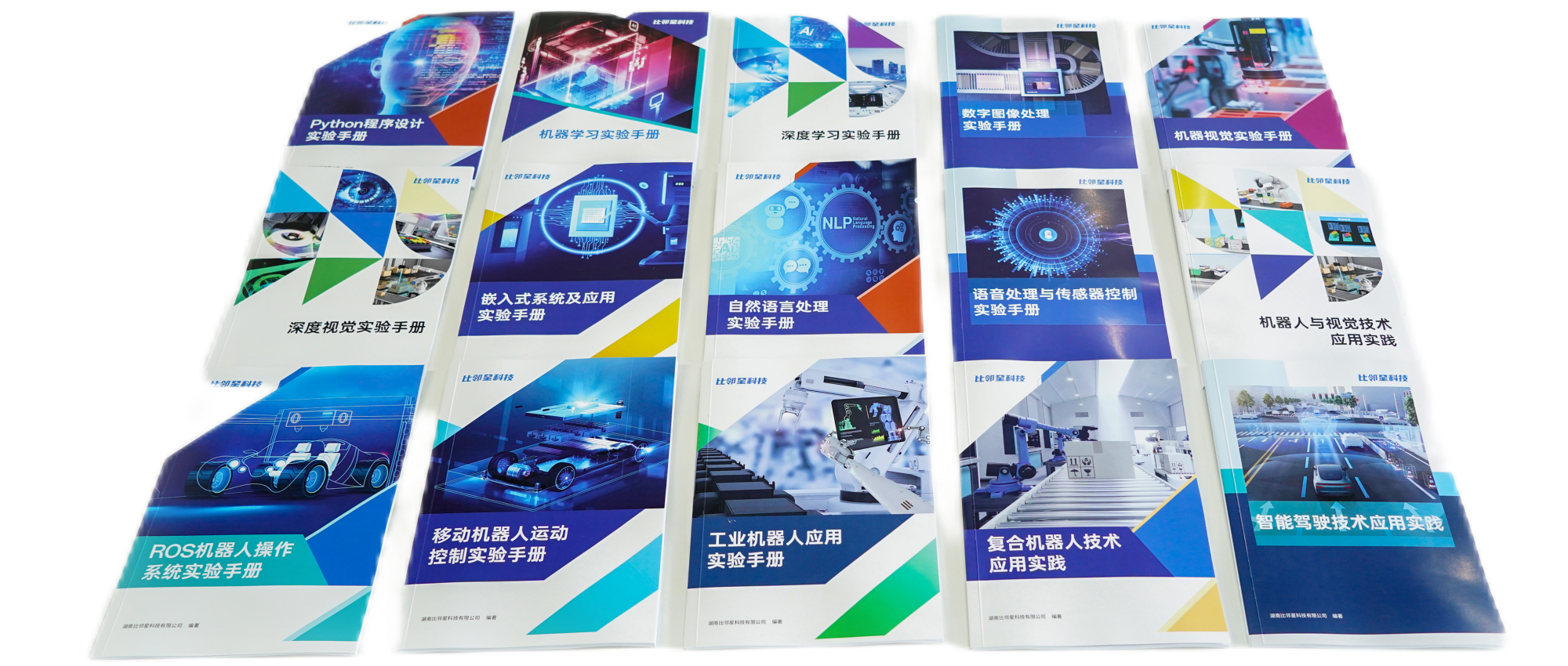
(1) ROS Operating System Configuration
(2) Creation and Compilation of ROS Packages
(3) ROS Messages and Services
(4) ROS Message Publishers and Subscribers
(5) Server and Client
(6) Definition and Usage of Topic Messages
(7) ROS Use in Multi-Robot Systems
(1) Introduction to Robot Systems
(2) Describing Robot Spatial Pose
(3) Establishing Link Coordinate Systems and D-H Parameters
(4) Robot Forward Kinematics
(5) Robot Inverse Kinematics
(6) Robot Joint Space Planning
(7) Robot Cartesian Space Planning
(8) Robot Jacobian Matrix
(9) Robot Dynamics
(10) Robot Dynamic Parameter Identification
(11) Robot Drag Teaching
(12) Drag Teaching Experiment Based on End-Effector Torque Sensors
(1) Recognition of Six-Axis Robot Multi-Mechanical Structures
(2) Coordinate Transformation of Six-Axis Robots
(3) Six-Axis Robot Six-Axis Coordinated Control
(4) Six-Axis Robot Teaching Programming Control
(5) Six-Axis Robot Trajectory Path Programming
(1) Introduction to Vision Systems
(2) Object Localization and Angle Measurement
(3) Edge Length Measurement and Area Detection
(4) Object Color and Shape Recognition
(5) Barcode and QR Code Recognition
(6) OCR Character Segmentation and Recognition
(7) Product Surface Defect Detection Based on Morphological Processing
(8) License Plate Recognition
(9) Electronic Product Recognition Based on Template Matching
(1) Six-Axis Robot Recognition and Basic Operation
(2) Calibration of Six-Axis Robots with Vision Systems
(3) Vision-Based Six-Axis Robot Object Classification
(4) Vision-Based Six-Axis Robot Object Palletizing
(5) Vision-Based Six-Axis Robot Digital Sorting
(6) Vision-Based Six-Axis Robot Fruit Classification
Contact us if you need a custom course.
Expandability
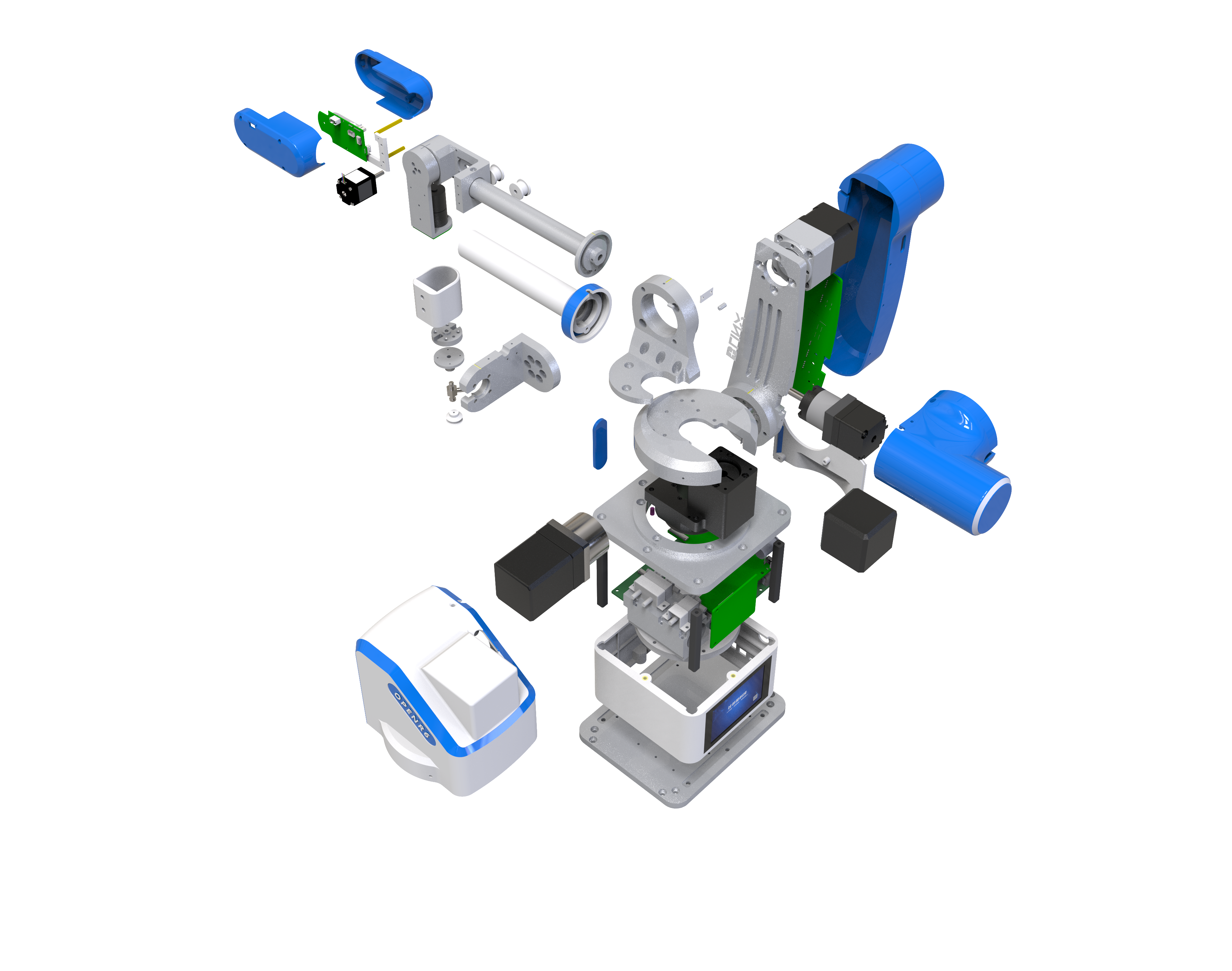
Assembleable
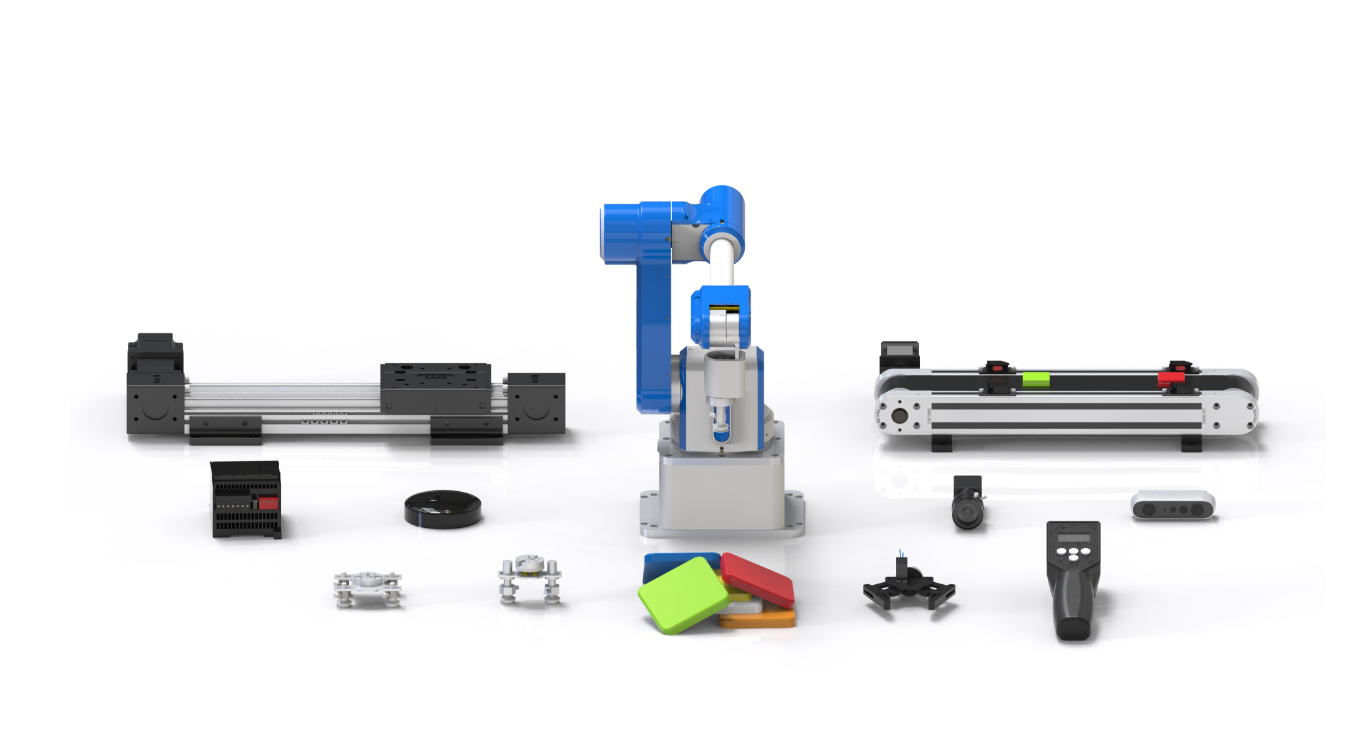
Versatile
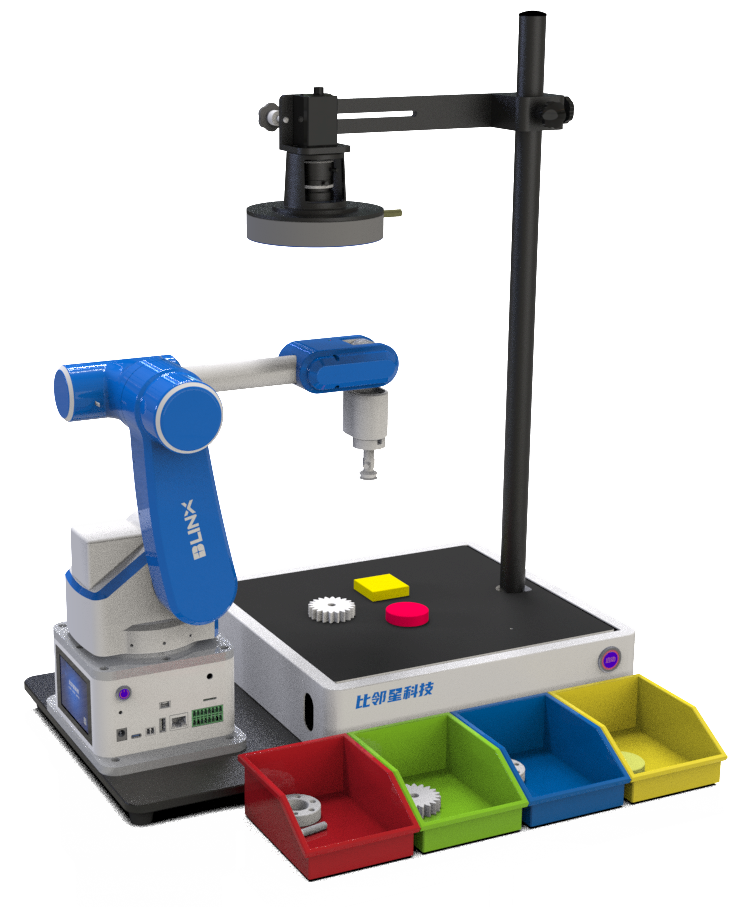
Structure 1
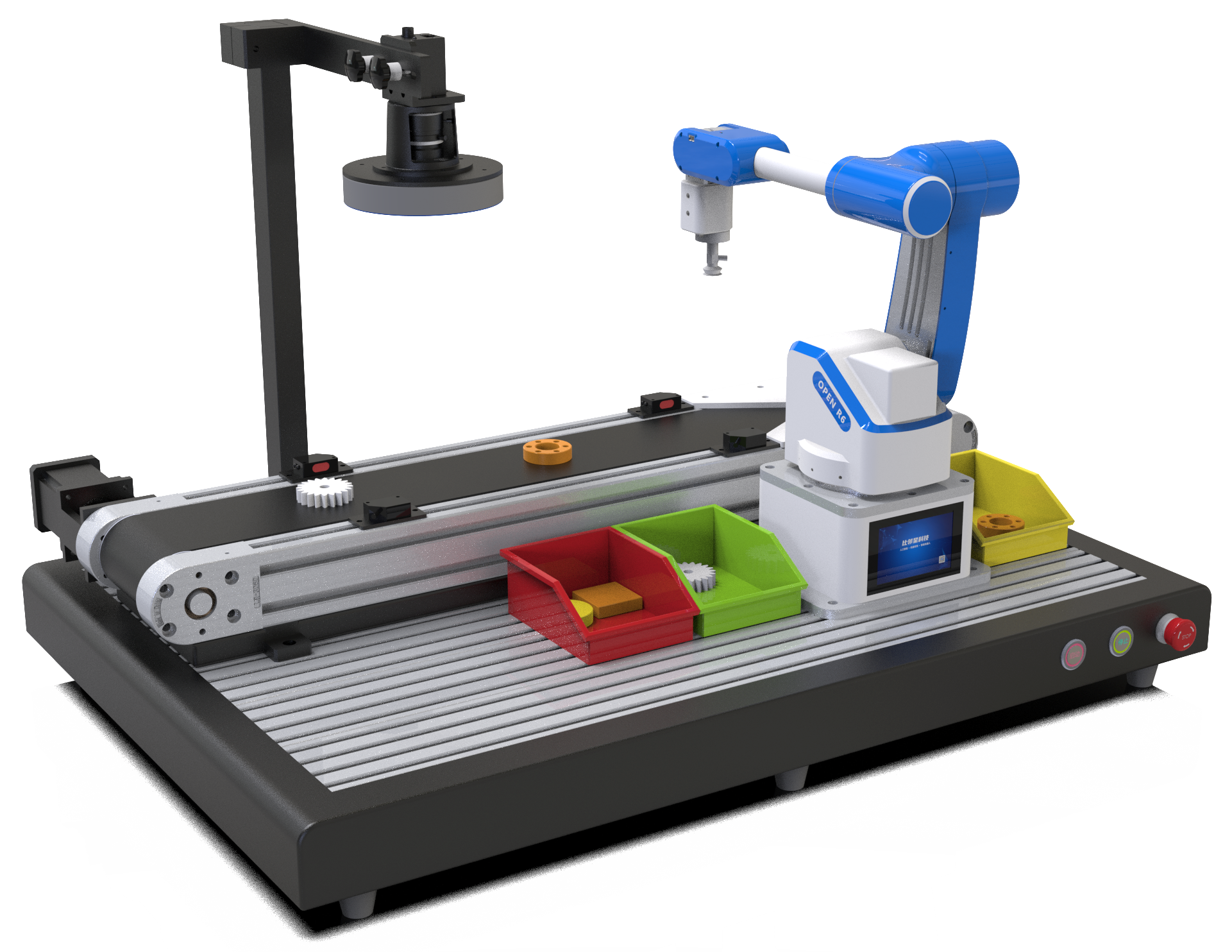
Structure 2
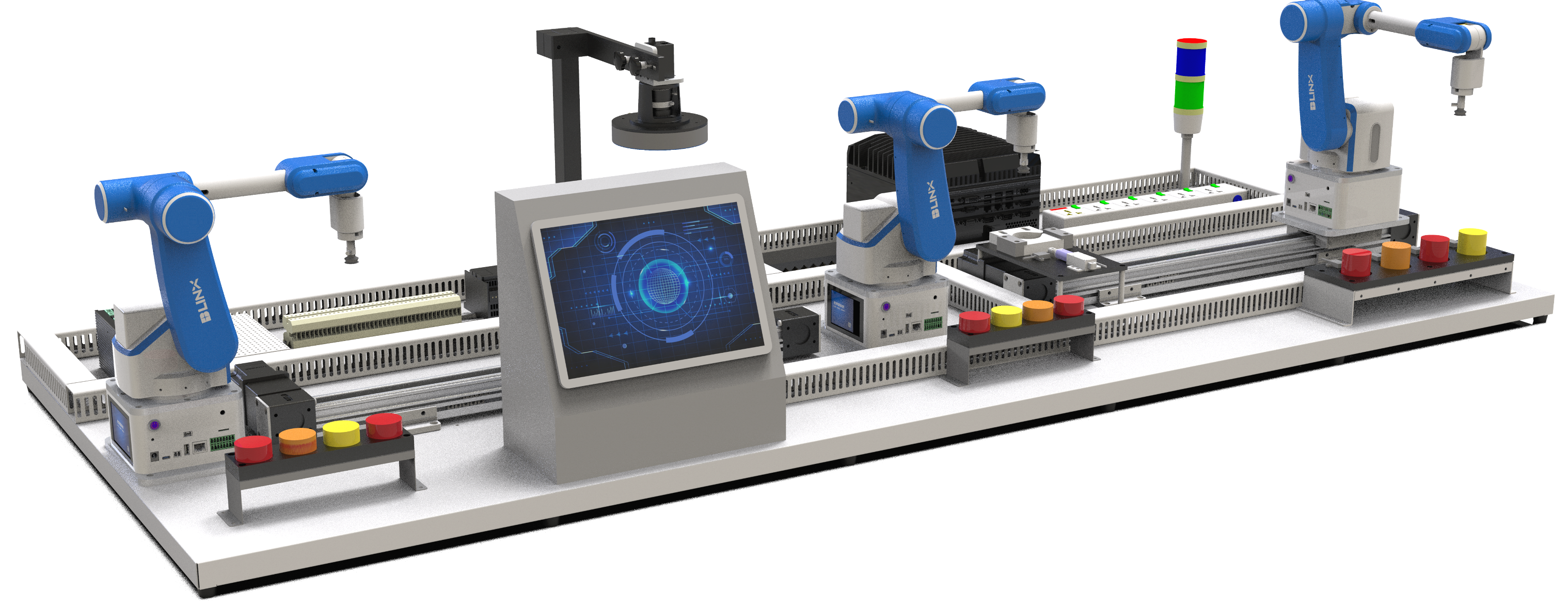
Structure 3
FAQ
1.What is a 6-axis robotic arm?
2.What is the working accuracy of the 6-axis robotic arm?
3.What is the payload capacity of the 6-axis robotic arm?
4.Does the 6-axis robotic arm support multi-robot collaboration?
5.How is the 6-axis robotic arm programmed and operated?
6.Is the 6-axis robotic arm suitable for beginners?
7.Is the 6-axis robotic arm open-source?
8.What types of experiments or tasks is the 6-axis robotic arm suitable for?
9.Does the device require professional installation and setup?
10.How can I access technical support or after-sales service?
Download
Please submit your download request, and we will send the relevant information to your email within 2 business days.